计算机辅助工艺过程设计也被译为计算机辅助生产流程设计。国际生产工程研究会提出了计算机辅助规划、计算机自动化生产流程设计(CAPP)等名称,由于计算机集成制造系统的出现,工艺规划开始与计算机辅助设计(CAD)及计算机辅助制造(CAM)相连,成为连接设计与制造的间的桥梁,设计信息可通过工艺规划生成制造信息。
生产规划
传统的生产规划包括制作产生原料与生产组装所需零件的流程的一切数据,工程师必须决定原料的组成、加工顺序等等。而以上这些零碎的问题可简单地区分为三类:产品(Product)、流程(Process)、资源(Resource)。以往我们靠个人工艺来完成产品,其间所需的资源及流程则是由老师傅自行决定,但走入大量制造的时代后,产品逐渐复杂化且多样化,而这类产品是需要多人完成的产品,例如飞机、船舶、车辆等,为使更多的人能理解产品的结构,并制造出我们所需的产品,我们必须提供足够的信息来对其进行描述产品、流程、资源,藉此交流、理解后才能有效率的工作。而自1970年代以来,计算机辅助工艺过程设计(CAPP - Computer Aided Process Planning)开始发展,该技术的运用是利用计算机的逻辑与人工智能(经验)来协助工程师进行工艺规划。
工艺规划
工艺规划是依据产品设计图与施工說明决定加工作业顺序。由于一般的设计图只有标示产品的最终尺寸、公差、形状与使用材料等信息,并没有说明加工的方法、使用的机器及加工的步骤等,因此,必须先订定出最经济有效的加工方法与顺序,以供所有操作人员有所遵循。
换言之,工艺规划是用来规划「自原料开始到加工,以至于产品完成期间」所经过最经济有效的加工途径,使成本最低、效率最高、质量最适当之一项计划。其影响的因素包括:「生产形态」、「机器设备的性能」、「机器设备的负荷与产能」、「员工的安排」、「标准化作业的建立」等。
工艺规划的设计程序如下:
• 决定生产的程序
对于装配性的产品,可由产品装配图或操作程序图来设定其生产的程序;对于加工性的产品,则需由有经验的工艺技术
人员,依产品使用的原材料形状、加工步骤与方法,逐一列出完整的生产程序。
由于生产程序的拟定因人而异,即便是同一个产品也可能因技术人员的不同而订出不同的生产程序,因此企业必须依最
佳的程序来决定标准的生产程序。
• 决定每一工艺所用的机器与工具
考虑机器的产能、加工能力与负荷以决定所使用的机器,而选择机器时,除了考虑经济性及最低成本外,应同时考虑各
机器间的负荷平衡,以使生产时能有最佳的效率。
• 决定所需材料型态与数量
材料的材质应已于设计时间指定,但材料的尺寸及样式,则必须配合加工方式及机器设备来决定,而所需材料数量则由
产品所展开的物料清单( Bill of Material,BOM)来决定。
• 决定操作人力与时间
由标准操作方法、机器的能力、再配合工作研究与时间研究,来决定每一项作业所需的人员数目与作业时间。
• 决定检验点
决定生产程序中,于何时、何项作业、作何种的检验项目,以确保所生产的产品符合规格要求。
计算机辅助工艺规划
计算机辅助工艺规划(CAPP)是通过向计算机输入被加工零件的原始信息,加工条件和加工要求,由计算机自动地进行编码,撰写程序直至最后输出为经过优化的工艺卡片的过程。在集成性CAD/CAPP/CAM系统中,由于设计时在共享数据库中所建立的产品模型不仅仅包含了几何数据,也记录了有关生产需要的数据,以供计算机辅助工艺规划利用。计算机辅助工艺规划的设计结果也存回公共数据库中供CAM的数控程序。集成性的作用不仅仅在于节省了人工传递信息和数据,更有利于产品生产的整体考虑。从共享数据库中,设计工程师可以获得并考察其所设计产品的加工信息,制造工程师可以从中清楚地知道产品的设计需求。全面地考察这些信息,可以使产品生产获得更大的效益。
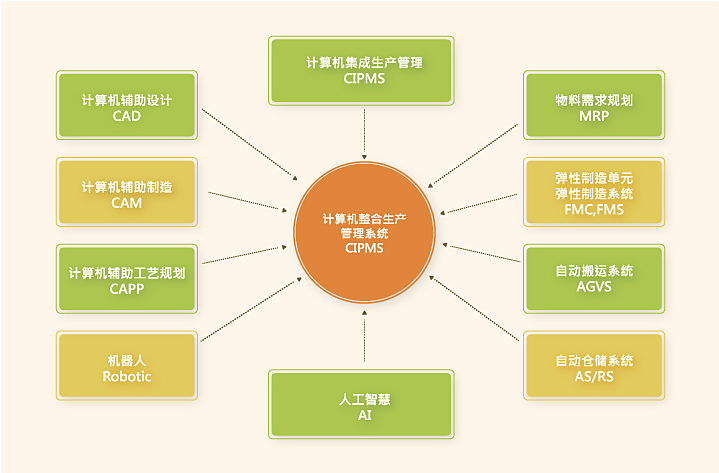
►本文内容摘自网络文章-生产计划与管制,页4-5并加以整理。
生产规划
传统的生产规划包括制作产生原料与生产组装所需零件的流程的一切数据,工程师必须决定原料的组成、加工顺序等等。而以上这些零碎的问题可简单地区分为三类:产品(Product)、流程(Process)、资源(Resource)。以往我们靠个人工艺来完成产品,其间所需的资源及流程则是由老师傅自行决定,但走入大量制造的时代后,产品逐渐复杂化且多样化,而这类产品是需要多人完成的产品,例如飞机、船舶、车辆等,为使更多的人能理解产品的结构,并制造出我们所需的产品,我们必须提供足够的信息来对其进行描述产品、流程、资源,藉此交流、理解后才能有效率的工作。而自1970年代以来,计算机辅助工艺过程设计(CAPP - Computer Aided Process Planning)开始发展,该技术的运用是利用计算机的逻辑与人工智能(经验)来协助工程师进行工艺规划。
工艺规划
工艺规划是依据产品设计图与施工說明决定加工作业顺序。由于一般的设计图只有标示产品的最终尺寸、公差、形状与使用材料等信息,并没有说明加工的方法、使用的机器及加工的步骤等,因此,必须先订定出最经济有效的加工方法与顺序,以供所有操作人员有所遵循。
换言之,工艺规划是用来规划「自原料开始到加工,以至于产品完成期间」所经过最经济有效的加工途径,使成本最低、效率最高、质量最适当之一项计划。其影响的因素包括:「生产形态」、「机器设备的性能」、「机器设备的负荷与产能」、「员工的安排」、「标准化作业的建立」等。
工艺规划的设计程序如下:
• 决定生产的程序
对于装配性的产品,可由产品装配图或操作程序图来设定其生产的程序;对于加工性的产品,则需由有经验的工艺技术
人员,依产品使用的原材料形状、加工步骤与方法,逐一列出完整的生产程序。
由于生产程序的拟定因人而异,即便是同一个产品也可能因技术人员的不同而订出不同的生产程序,因此企业必须依最
佳的程序来决定标准的生产程序。
• 决定每一工艺所用的机器与工具
考虑机器的产能、加工能力与负荷以决定所使用的机器,而选择机器时,除了考虑经济性及最低成本外,应同时考虑各
机器间的负荷平衡,以使生产时能有最佳的效率。
• 决定所需材料型态与数量
材料的材质应已于设计时间指定,但材料的尺寸及样式,则必须配合加工方式及机器设备来决定,而所需材料数量则由
产品所展开的物料清单( Bill of Material,BOM)来决定。
• 决定操作人力与时间
由标准操作方法、机器的能力、再配合工作研究与时间研究,来决定每一项作业所需的人员数目与作业时间。
• 决定检验点
决定生产程序中,于何时、何项作业、作何种的检验项目,以确保所生产的产品符合规格要求。
计算机辅助工艺规划
计算机辅助工艺规划(CAPP)是通过向计算机输入被加工零件的原始信息,加工条件和加工要求,由计算机自动地进行编码,撰写程序直至最后输出为经过优化的工艺卡片的过程。在集成性CAD/CAPP/CAM系统中,由于设计时在共享数据库中所建立的产品模型不仅仅包含了几何数据,也记录了有关生产需要的数据,以供计算机辅助工艺规划利用。计算机辅助工艺规划的设计结果也存回公共数据库中供CAM的数控程序。集成性的作用不仅仅在于节省了人工传递信息和数据,更有利于产品生产的整体考虑。从共享数据库中,设计工程师可以获得并考察其所设计产品的加工信息,制造工程师可以从中清楚地知道产品的设计需求。全面地考察这些信息,可以使产品生产获得更大的效益。
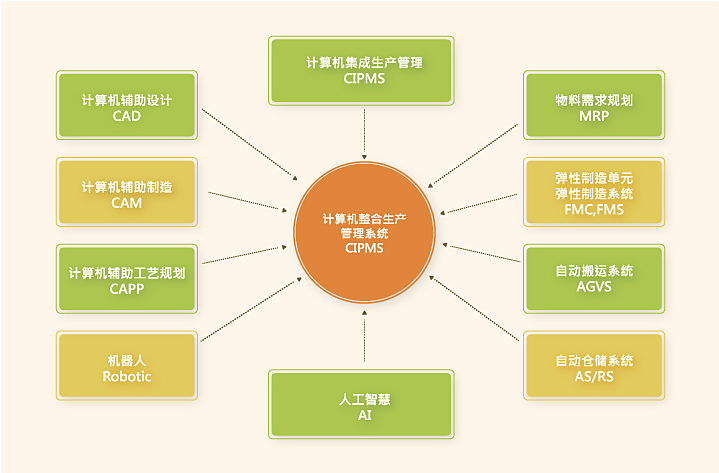
►本文内容摘自网络文章-生产计划与管制,页4-5并加以整理。