電腦輔助製程規劃也被譯為電腦輔助製造流程設計。國際生產工程研究會提出了電腦輔助規劃、電腦自動化製造流程設計(CAPP)等名稱,由於電腦整合製造系統的出現,製程規劃開始與電腦輔助設計(CAD)及電腦輔助製造(CAM)相連,成為連接設計與製造之間的橋梁,設計資訊可通過製程規劃生成製造資訊。
生產規劃
傳統的生產規劃包括製作產生原料與生產組裝所需零件之流程的一切資料,工程師必須決定原料的組成、加工順序等等。而以上這些零碎的問題可簡單地區分為三類:產品(Product)、流程(Process)、資源(Resource)。以往我們靠個人工藝來完成產品,其間所需的資源及流程則是由老師傅自行決定,但走入大量製造的時代後,產品逐漸複雜化且多樣化,而這類產品是需要多人完成的產品,例如飛機、船舶、車輛等,為使更多的人能理解產品的結構,並製造出我們所需的產品,我們必須提供足夠的資訊來對其進行描述產品、流程、資源,藉此交流、理解後才能有效率的工作。而自1970年代以來,電腦輔助製程規劃(CAPP - Computer Aided Process Planning)開始發展,該技術的運用是利用電腦的邏輯與人工智慧(經驗)來協助工程師進行製程規劃
製程規劃
製程規劃是依據產品設計圖與施工說明決定加工作業順序。由於一般的設計圖只有標示產品的最終尺寸、公差、形狀與使用材料等資訊,並沒有說明加工的方法、使用的機器及加工的步驟等,因此,必須先訂定出最經濟有效的加工方法與順序,以供所有操作人員有所遵循。
換言之,製程規劃是用來規劃「自原料開始到加工,以至於產品完成期間」所經過最經濟有效的加工途徑,使成本最低、效率最高、品質最適當的一項計畫。其影響的因素包括:「生產型態」、「機器設備的性能」、「機器設備的負荷與產能」、「員工的安排」、「標準化作業的建立」等。
製程規劃的設計程序如下:
• 決定生產的程序
對於裝配性的產品,可由產品裝配圖或操作程序圖來設定其生產的程序;對於加工性的產品,則需由有經驗的製程技術人員,依產品使用的原材料形狀、加工步驟與方法,逐一列出完整的生產程序。 由於生產程序的擬定因人而異,即便是同一個產品也可能因技術人員的不同而訂出不同的生產程序,因此企業必須依最佳的程序來決定標準的生產程序。
• 決定每一製程所用的機器與工具
考慮機器的產能、加工能力與負荷以決定所使用的機器,而選擇機器時,除了考慮經濟性及最低成本外,應同時考慮各機器間的負荷平衡,以使生產時能有最佳的效率。
• 決定所需材料型態與數量
材料的材質應已於設計階段指定,但材料的尺寸及型式,則必須配合加工方式及機器設備來決定,而所需材料數量則由產品所展開的物料清單( Bill of Material,BOM)來決定。
• 決定操作人力與時間
由標準操作方法、機器的能力、再配合工作研究與時間研究,來決定每一項作業所需的人員數目與作業時間。
• 決定檢驗點
決定生產程序中,於何時、何項作業、作何種的檢驗項目,以確保所生產的產品符合規格要求。
電腦輔助製程規劃
電腦輔助製程規劃(CAPP)是透過向電腦輸入被加工零件的原始資訊,加工條件和加工要求,由電腦自動地進行編碼,撰寫程式直至最後輸出為經過優化的工藝卡片的過程。在整合性CAD/CAPP/CAM系統中,由於設計時在共用資料庫中所建立的產品模型不僅僅包含了幾何數據,也記錄了有關生產需要的數據,以供電腦輔助製程規劃利用。電腦輔助製程規劃的設計結果也存回公共資料庫中供CAM的數控程式。整合性的作用不僅僅在於節省了人工傳遞資訊和資料,更有利於產品生產的整體考慮。從共用資料庫中,設計工程師可以獲得並考察他所設計產品的加工資訊,製造工程師可以從中清楚地知道產品的設計需求。全面地考察這些信息,可以使產品生產獲得更大的效益。
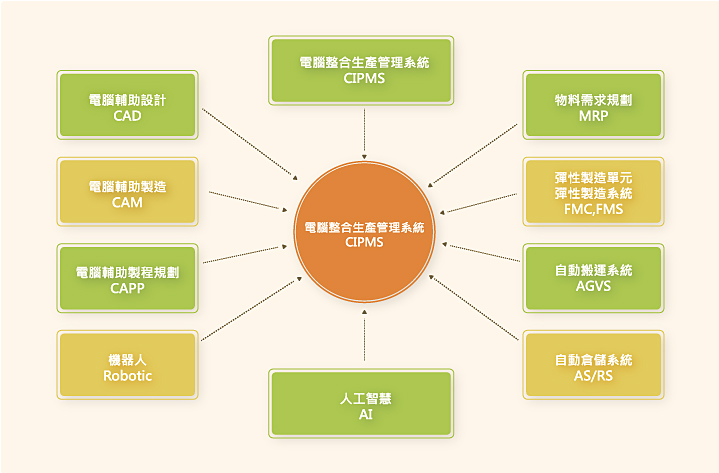
►本文內容摘自網路文章-生產計畫與管制,頁4-5並加以整理。
生產規劃
傳統的生產規劃包括製作產生原料與生產組裝所需零件之流程的一切資料,工程師必須決定原料的組成、加工順序等等。而以上這些零碎的問題可簡單地區分為三類:產品(Product)、流程(Process)、資源(Resource)。以往我們靠個人工藝來完成產品,其間所需的資源及流程則是由老師傅自行決定,但走入大量製造的時代後,產品逐漸複雜化且多樣化,而這類產品是需要多人完成的產品,例如飛機、船舶、車輛等,為使更多的人能理解產品的結構,並製造出我們所需的產品,我們必須提供足夠的資訊來對其進行描述產品、流程、資源,藉此交流、理解後才能有效率的工作。而自1970年代以來,電腦輔助製程規劃(CAPP - Computer Aided Process Planning)開始發展,該技術的運用是利用電腦的邏輯與人工智慧(經驗)來協助工程師進行製程規劃
製程規劃
製程規劃是依據產品設計圖與施工說明決定加工作業順序。由於一般的設計圖只有標示產品的最終尺寸、公差、形狀與使用材料等資訊,並沒有說明加工的方法、使用的機器及加工的步驟等,因此,必須先訂定出最經濟有效的加工方法與順序,以供所有操作人員有所遵循。
換言之,製程規劃是用來規劃「自原料開始到加工,以至於產品完成期間」所經過最經濟有效的加工途徑,使成本最低、效率最高、品質最適當的一項計畫。其影響的因素包括:「生產型態」、「機器設備的性能」、「機器設備的負荷與產能」、「員工的安排」、「標準化作業的建立」等。
製程規劃的設計程序如下:
• 決定生產的程序
對於裝配性的產品,可由產品裝配圖或操作程序圖來設定其生產的程序;對於加工性的產品,則需由有經驗的製程技術人員,依產品使用的原材料形狀、加工步驟與方法,逐一列出完整的生產程序。 由於生產程序的擬定因人而異,即便是同一個產品也可能因技術人員的不同而訂出不同的生產程序,因此企業必須依最佳的程序來決定標準的生產程序。
• 決定每一製程所用的機器與工具
考慮機器的產能、加工能力與負荷以決定所使用的機器,而選擇機器時,除了考慮經濟性及最低成本外,應同時考慮各機器間的負荷平衡,以使生產時能有最佳的效率。
• 決定所需材料型態與數量
材料的材質應已於設計階段指定,但材料的尺寸及型式,則必須配合加工方式及機器設備來決定,而所需材料數量則由產品所展開的物料清單( Bill of Material,BOM)來決定。
• 決定操作人力與時間
由標準操作方法、機器的能力、再配合工作研究與時間研究,來決定每一項作業所需的人員數目與作業時間。
• 決定檢驗點
決定生產程序中,於何時、何項作業、作何種的檢驗項目,以確保所生產的產品符合規格要求。
電腦輔助製程規劃
電腦輔助製程規劃(CAPP)是透過向電腦輸入被加工零件的原始資訊,加工條件和加工要求,由電腦自動地進行編碼,撰寫程式直至最後輸出為經過優化的工藝卡片的過程。在整合性CAD/CAPP/CAM系統中,由於設計時在共用資料庫中所建立的產品模型不僅僅包含了幾何數據,也記錄了有關生產需要的數據,以供電腦輔助製程規劃利用。電腦輔助製程規劃的設計結果也存回公共資料庫中供CAM的數控程式。整合性的作用不僅僅在於節省了人工傳遞資訊和資料,更有利於產品生產的整體考慮。從共用資料庫中,設計工程師可以獲得並考察他所設計產品的加工資訊,製造工程師可以從中清楚地知道產品的設計需求。全面地考察這些信息,可以使產品生產獲得更大的效益。
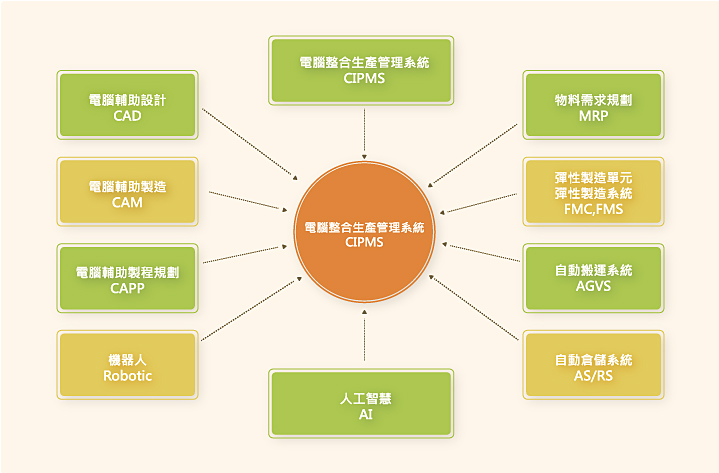
►本文內容摘自網路文章-生產計畫與管制,頁4-5並加以整理。